CNC Precision Machining Manufacturers: A Comprehensive Overview
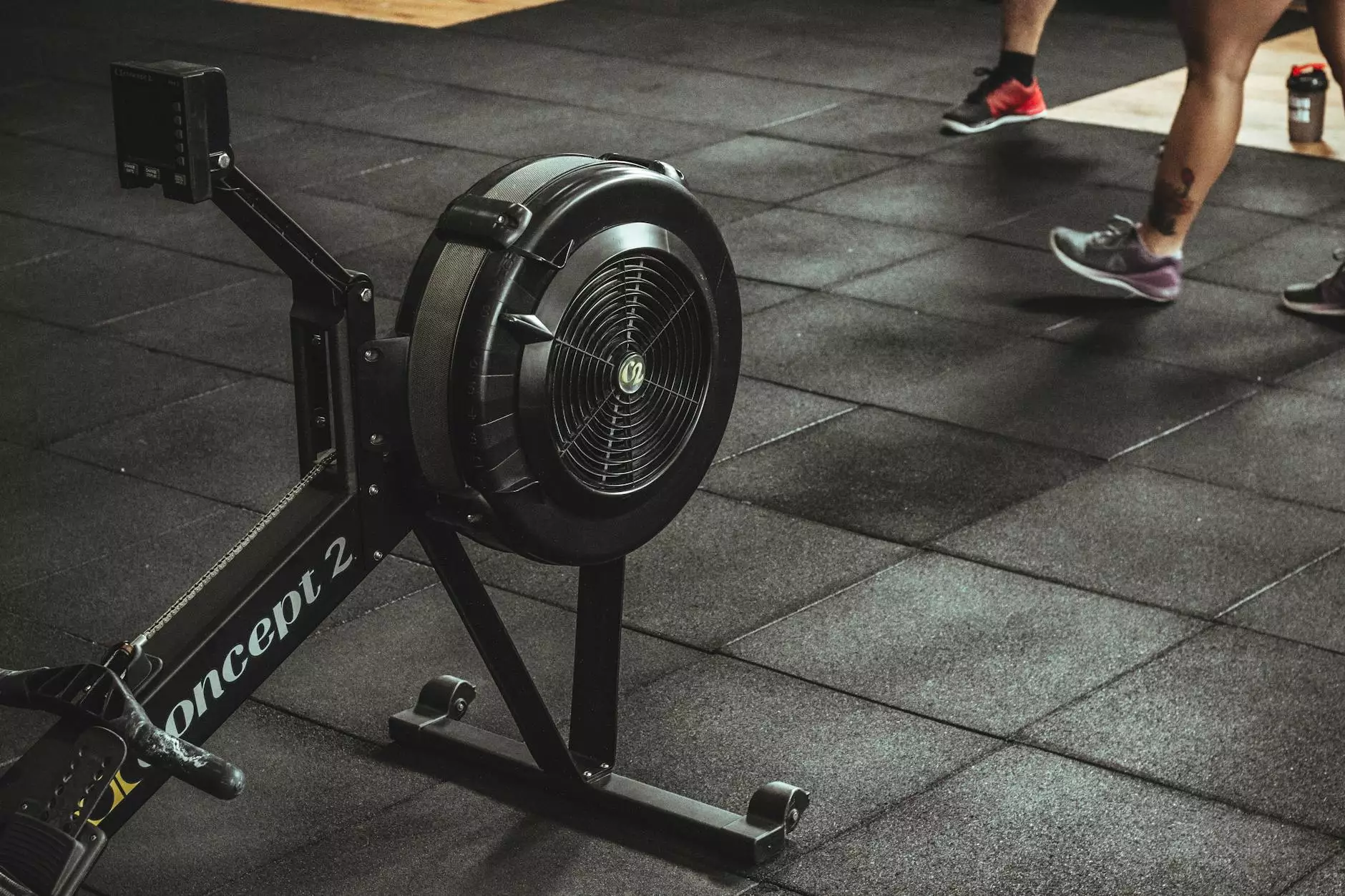
CNC (Computer Numerical Control) precision machining is a cornerstone of contemporary manufacturing, transforming raw materials into intricate components that meet exact specifications. This article delves deep into the realm of cnc precision machining manufacturers, explaining their significance, processes, technologies, and applications.
Understanding CNC Precision Machining
CNC precision machining involves utilizing computer-controlled tools to manufacture parts and components from various materials including metals, plastics, and composites. These processes ensure high precision, repeatability, and efficiency in production.
The Fundamentals of CNC Machining
- Computer Control: CNC machines operate based on programmed instructions crafted using CAD (Computer-Aided Design) software. This allows manufacturers to produce complex shapes with high accuracy.
- Various Machining Techniques: CNC machining encompasses several processes such as turning, milling, drilling, and grinding, each tailored for specific applications.
- Automation and Efficiency: Automating the machining process reduces human error and increases production speed, enabling manufacturers to meet large-scale demands.
The Role of CNC Precision Machining Manufacturers
CNC precision machining manufacturers play an essential role in the supply chain of numerous industries. From automotive to aerospace, their expertise in creating high-quality, precision components cannot be overstated.
Key Responsibilities of CNC Precision Machining Manufacturers
- Material Selection: They choose appropriate materials based on mechanical properties and end-use requirements.
- Tooling and Fixture Design: Designing effective tools and fixtures that ensure optimal performance and precision during machining.
- Quality Assurance: Implementing rigorous quality control measures to ensure every part meets stringent specifications.
- Continuous Innovation: Staying updated with the latest technologies and methodologies for improving machining processes.
Advantages of Using CNC Precision Machining
The benefits of CNC precision machining are significant, positioning it as a preferred choice for manufacturers. Here are some of the notable advantages:
- High Precision: CNC machines can produce intricate designs with tolerances as tight as +/- 0.001 inches.
- Repeatability: Once a design is programmed, manufacturers can produce identical components in large quantities.
- Complex Geometries: CNC machining can create shapes that would be impossible or highly impractical to achieve through traditional machining methods.
- Reduced Waste: Precise cutting leads to minimal waste of materials, contributing to overall cost-effectiveness.
- Scalability: From prototyping to full production runs, CNC machining accommodates varying production needs seamlessly.
Industry Applications of CNC Precision Machining
CNC precision machining is employed across diverse sectors, showcasing its versatility and importance:
1. Aerospace Industry
The aerospace sector demands components that meet strict safety and performance criteria. CNC machined parts, such as engine components, brackets, and housings, are fabricated with an exceptional level of precision that is crucial for flight safety.
2. Automotive Sector
In the automotive industry, CNC precision machining manufacturers produce parts ranging from engine blocks to intricate interior fittings. The ability to create lightweight yet strong components enhances vehicle performance and fuel efficiency.
3. Medical Applications
Medical devices and instruments often require parts that are not only precise but also biocompatible. CNC machined components like surgical instruments, implants, and housings for medical devices are vital to this industry.
4. Electronics Manufacturing
In electronics, CNC precision machining is used to create housings and support structures for components like circuit boards that require specific tolerances and finishes.
Choosing the Right CNC Precision Machining Manufacturer
Selecting the right cnc precision machining manufacturers involves various considerations. Here are key factors to evaluate:
1. Expertise and Experience
Investigate the manufacturer's experience in the industry, as established manufacturers tend to have a proven track record of delivering reliable products.
2. Technology and Equipment
Assess the technology and machinery utilized. Advanced equipment typically results in enhanced precision and capability to undertake complex projects.
3. Quality Control Standards
Effective quality control processes ensure that all products meet required specifications. Look for manufacturers that adhere to internationally recognized standards such as ISO 9001.
4. Customer Support and Communication
Strong customer service is crucial for maintaining a steady flow of information during the manufacturing process. Choose suppliers who are responsive and transparent.
Future Trends in CNC Precision Machining
The landscape of CNC precision machining is continually evolving. Some notable trends shaping the future of this industry include:
- Industry 4.0: Integration of IoT (Internet of Things) and data analytics enhances machine performance, predictive maintenance, and operational efficiency.
- Automation and Robotics: Increased automation reduces labor costs and improves production times while maintaining quality.
- Sustainable Manufacturing: Manufacturers are increasingly adopting eco-friendly practices, utilizing recyclable materials and reducing energy consumption.
- Advanced Materials: The use of new composite materials opens avenues for creating lighter and stronger components, particularly in industries like aerospace and automotive.
The Importance of Continuous Learning in CNC Precision Machining
To remain competitive, professionals in the CNC machining sector must engage in continuous learning. This includes keeping updated with:
- New Technologies: Being aware of innovations such as 5-axis machining, additive manufacturing, and artificial intelligence applications.
- Industry Trends: Understanding shifts in market demand and technology to adapt manufacturing processes accordingly.
- Regulatory Changes: Staying informed about industry standards and regulations that may affect production methods and material selection.
The Competitive Landscape of CNC Precision Machining Manufacturers
The competition among cnc precision machining manufacturers is fierce. Companies must differentiate themselves through:
1. Specialization
Focusing on specific industries or types of components can help manufacturers carve out a niche market, enabling them to specialize and excel in their chosen areas.
2. Customer Relationships
Building lasting relationships with clients contributes to repeat business and referrals. Providing exceptional customer service and support can be a significant competitive advantage.
3. Innovation
Constantly innovating processes and exploring new technologies can help a manufacturer stay ahead of the curve and provide more value to its customers.
Conclusion
CNC precision machining manufacturers play a pivotal role in modern manufacturing ecosystems, providing essential components across countless industries. Their commitment to precision, efficiency, and innovation positions them at the forefront of technological advancement. As industries continue to evolve, so too will the capabilities and importance of CNC machining. By choosing knowledgeable, experienced, and technologically adept manufacturers, businesses can ensure quality components that meet their precise needs—paving the way for success in an increasingly competitive landscape.
For manufacturers looking to partner with a trusted CNC precision machining supplier, Deep Mould stands out as a leader in the field. Their dedication to quality and customer satisfaction makes them an ideal choice for any precision machining needs.