The Power of Die Casting and Injection Moulding in Modern Manufacturing
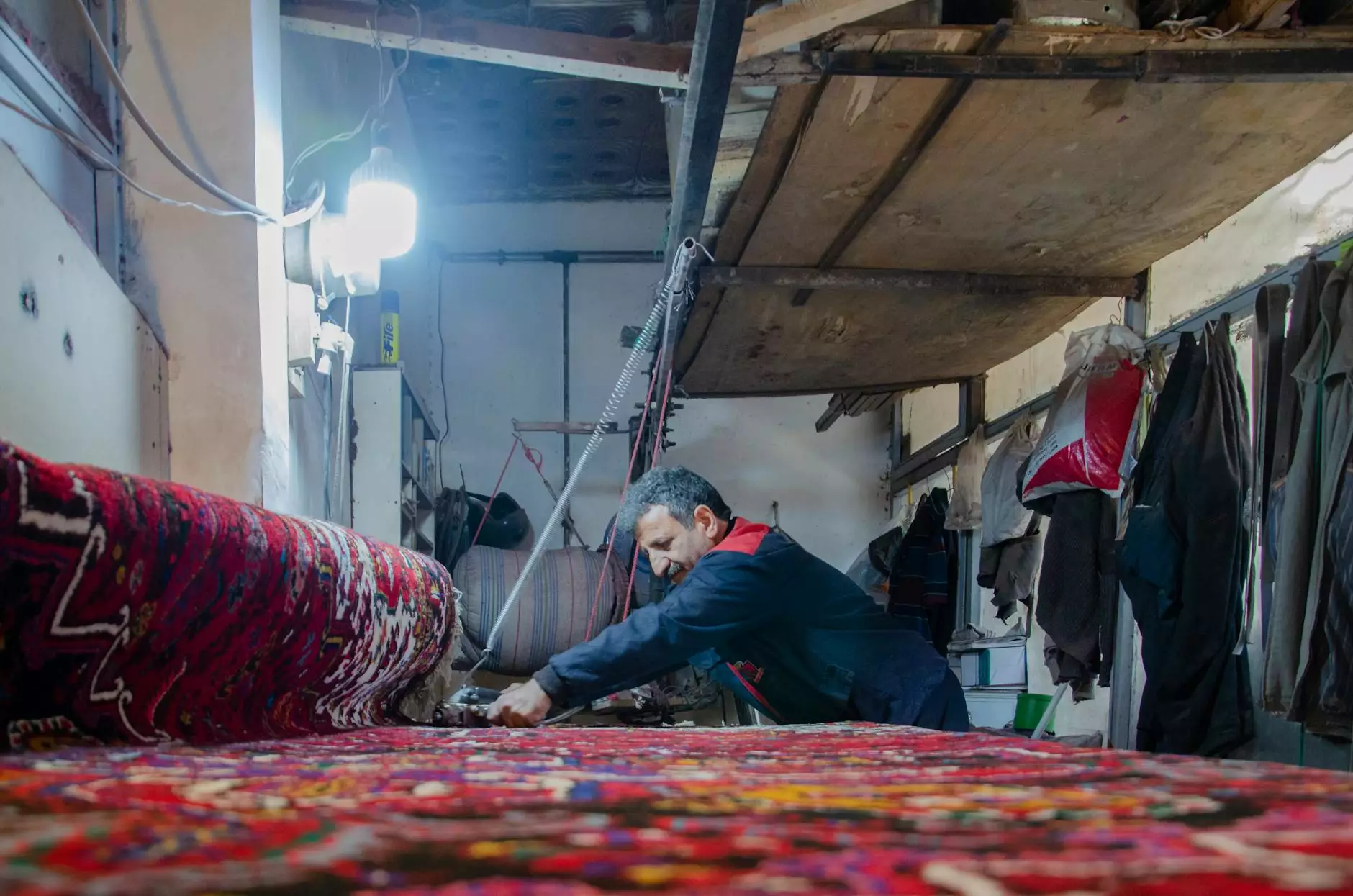
In today’s competitive manufacturing landscape, companies are continually seeking innovative methods to improve efficiency, reduce costs, and enhance the quality of their products. Among the various techniques available, die casting and injection moulding stand out as essential processes in the realm of metal fabrication. These methods not only streamline production but also offer incredible versatility across a range of industries.
What is Die Casting?
Die casting is a manufacturing process that involves forcing molten metal into a mold cavity under high pressure. This technique is primarily used for non-ferrous metals such as aluminum, zinc, and magnesium. The process begins with melting the metal and then injecting it into a pre-designed mold, which is then cooled to allow the metal to solidify into the desired shape.
Benefits of Die Casting
- Precision and Detail: Die casting allows for the production of intricate shapes and components with high tolerance levels.
- High Efficiency: The process can be automated, greatly enhancing production speeds and reducing labor costs.
- Surface Finish: Parts produced through die casting often require minimal finishing, reducing additional manufacturing steps.
- Material Conservation: The process minimizes waste, as excess material can often be reused.
- Strength and Durability: Components created through die casting exhibit excellent mechanical properties, making them ideal for demanding applications.
What is Injection Moulding?
Injection moulding is a manufacturing process primarily used for producing parts by injecting molten material into a mould. While frequently associated with plastics, this process can also be adapted for use with metals. In the case of die casting and injection moulding, the materials would typically be metals or metal-based alloys, enabling a wider range of applications and improved product performance.
Advantages of Injection Moulding
- Complex Geometries: Injection moulding facilitates the creation of highly complex parts that would be challenging to produce using other methods.
- High Production Rates: The process is designed for mass production, making it perfect for industries needing a large quantity of identical components.
- Material Versatility: A variety of materials can be used, including thermoplastics, thermosets, and metals, broadening its application scope.
- Consistent Quality: The precision of injection moulding ensures that each part produced is uniform, minimizing variations.
- Reduced Waste: Like die casting, injection moulding is efficient in material use, generating minimal scrap rates.
Comparing Die Casting and Injection Moulding
When evaluating die casting and injection moulding, it is essential to consider the differences between the two to determine which is better suited for specific applications. Both processes have unique advantages and are often selected based on the material being used, the required precision, and the production volume needed.
Key Differences
- Material Compatibility: Die casting is primarily for metals, while injection moulding is often dominated by plastics.
- Production Costs: Die casting has higher initial set-up costs but is more economical for large production runs, whereas injection moulding may have lower tooling costs for smaller runs.
- Finish and Tolerance: Die casting offers a superior finish and tighter tolerances compared to injection moulding.
- Parts Lifespan: Parts created through die casting typically have a longer lifespan due to their material properties and finish.
Applications of Die Casting and Injection Moulding
The industries that benefit from die casting and injection moulding processes are vast and varied. Here are some key sectors utilizing these methods effectively:
Aerospace Industry
In the aerospace industry, both die casting and injection moulding are essential for producing lightweight, high-strength components such as engine parts, housing, and structural elements. These processes contribute to improving fuel efficiency and overall performance.
Automotive Sector
The automotive sector is one of the largest consumers of die cast and injection moulded products. With the continuous push for lighter vehicles, manufacturers rely on these processes to produce components such as dashboards, engine housings, and various interior and exterior parts.
Consumer Electronics
Within the consumer electronics industry, die casting and injection moulding are crucial for producing housings and enclosures that protect delicate electronic components while providing aesthetic appeal.
Medical Devices
Medical devices require high precision and compliance with strict regulatory standards. Both die casting and injection moulding provide the ability to produce reliable and accurate parts integral to the functionality of various medical technologies.
Household Items
From kitchen appliances to furniture fittings, these manufacturing processes play a vital role in creating durable and affordable household items, enhancing consumer accessibility while maintaining high-quality standards.
The Future of Die Casting and Injection Moulding
As technology continues to evolve, the future of die casting and injection moulding looks promising. Advanced techniques such as 3D printing and the integration of smart manufacturing technologies are paving the way for these traditional processes to become even more efficient and versatile.
Innovations on the Horizon
- Automation: Incorporating robotics and automated systems will streamline production lines and reduce labor costs.
- Material Advancements: Developing new alloys and composite materials will expand the capabilities and applications of both processes.
- Sustainability: Emphasis on environmentally friendly practices will lead to improvements in material recycling and waste reduction.
- Customization: Enhanced digital technologies will allow for more customized solutions tailored to specific client needs.
Conclusion
Die casting and injection moulding are transformative processes in the field of metal fabrication and manufacturing. They deliver significant advantages, including efficiency, precision, versatility, and cost-effectiveness, that are pivotal for various industries. As technology progresses, these methods will become even more efficient and relevant, continuing to shape the future of manufacturing.
If you are exploring potential manufacturing processes for your products, consider the expertise available at deepmould.net. Their knowledge in die casting and injection moulding can provide you with the guidance necessary to make informed decisions that will benefit your business in the competitive landscape.